Develop an industrial resolver (rotation angle sensor) using your own technology.
Develop an industrial resolver (rotation angle sensor) using your own technology.
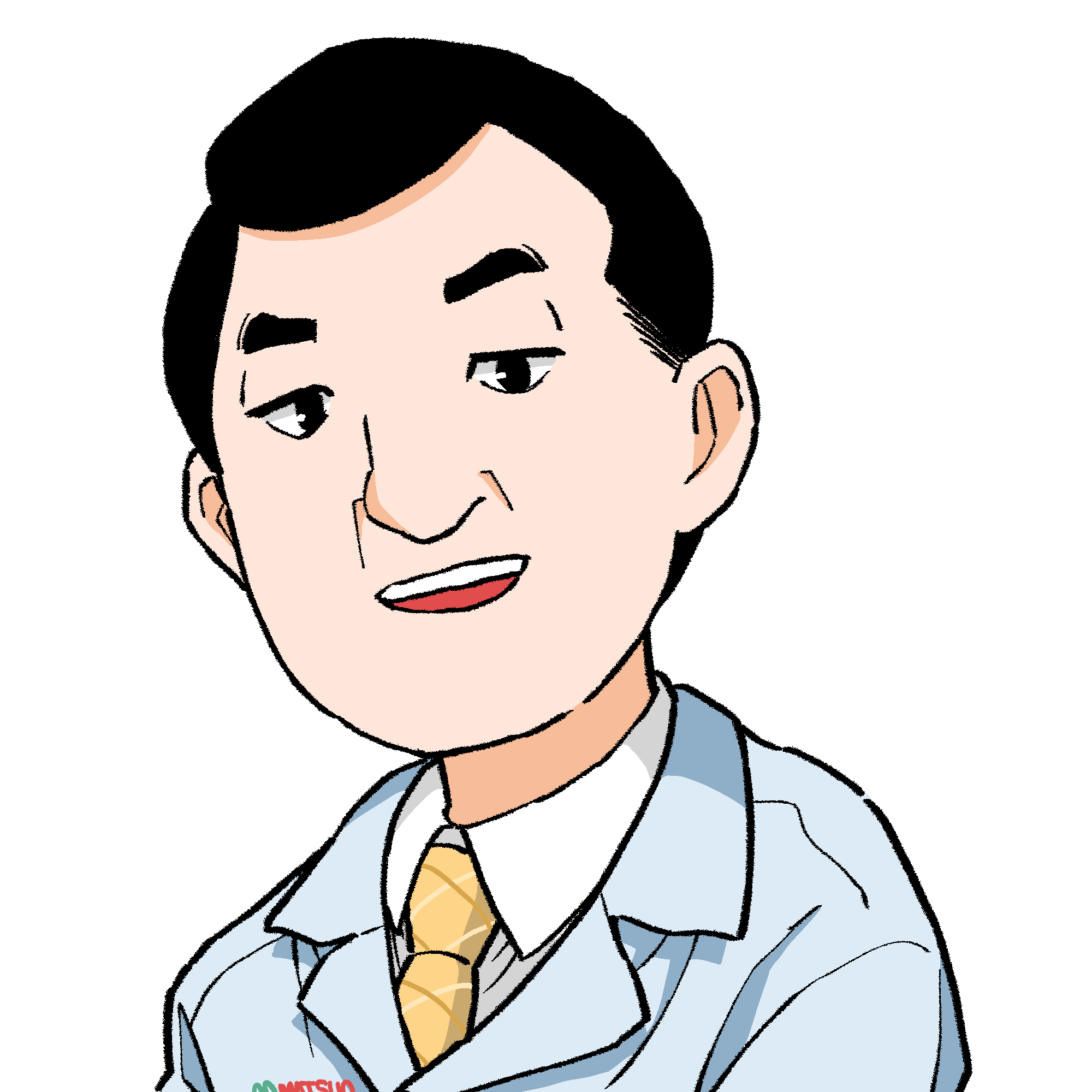
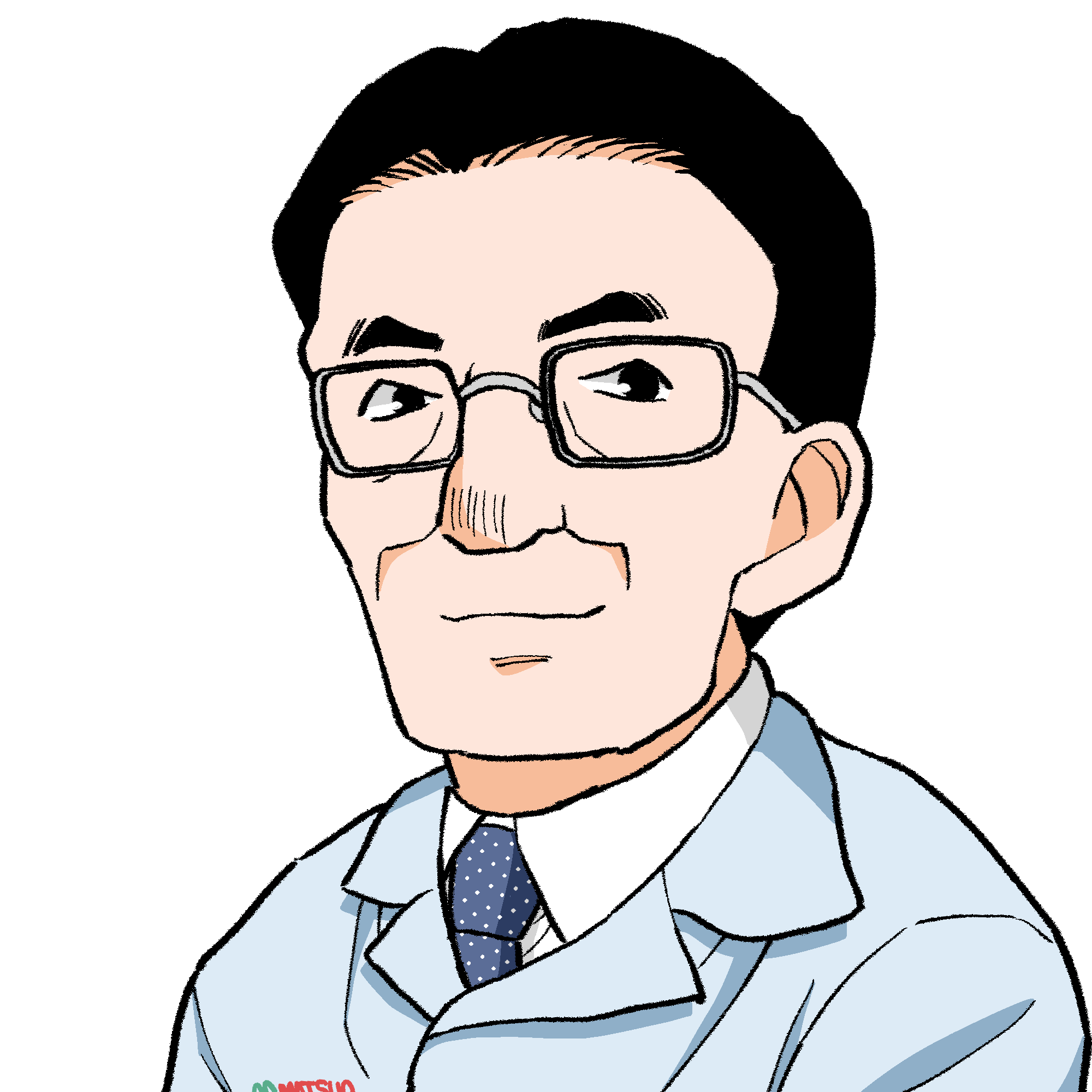
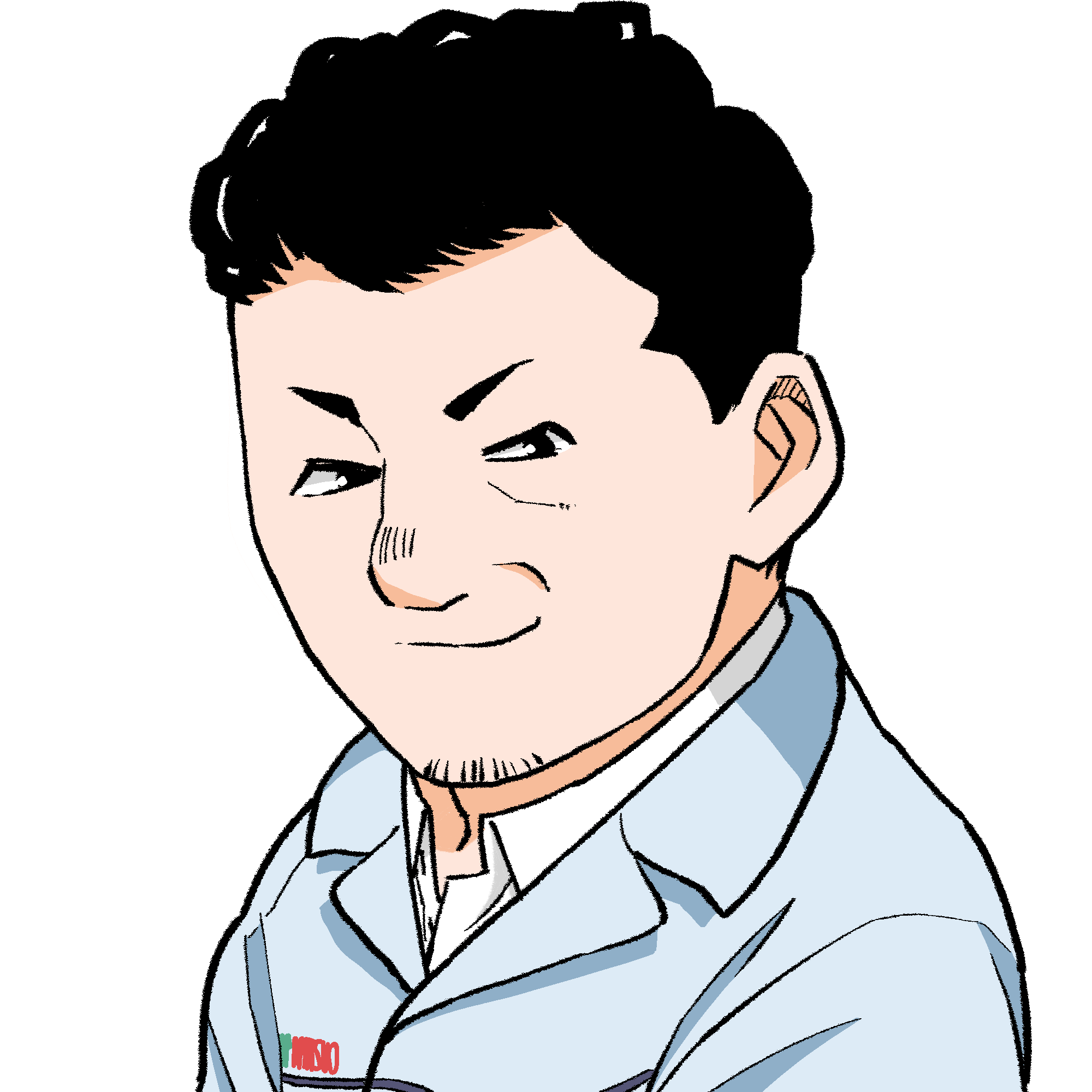
outlineMATSUO’S Project
Resolver development started more than a decade ago with only two people.
Yamakawa:
In fact, the development of the resolver itself started more than 10 years ago, initially with only two people, neither Mr. Tagawa nor Mr. Adachi. What could we do by fusing our existing technologies of “springs,” “pressed products,” and “insulators” with our developing technology of “sensor components”? Such an idea was the impetus for the development, but at the beginning, we did not yet have the image of developing into such a project team. Gradually, the number of people in the development section increased, and we have been working on the “development of industrial resolvers,” which is the project we are working on now, for about five years.
Tagawa:
For the project, a team was formed with members from development, sales, and prototyping. The prototype I was in charge of was to assemble the prototype designed by development with Mr. Yamakawa and Mr. Adachi to make it into a finished product. I had experience in the past as a participant in the start-up of mass production of new products, so I was highly motivated to make use of my abilities in this project. To tell you the truth, when I first joined the team, I started out not knowing anything about “resolvers” at all (laughs).
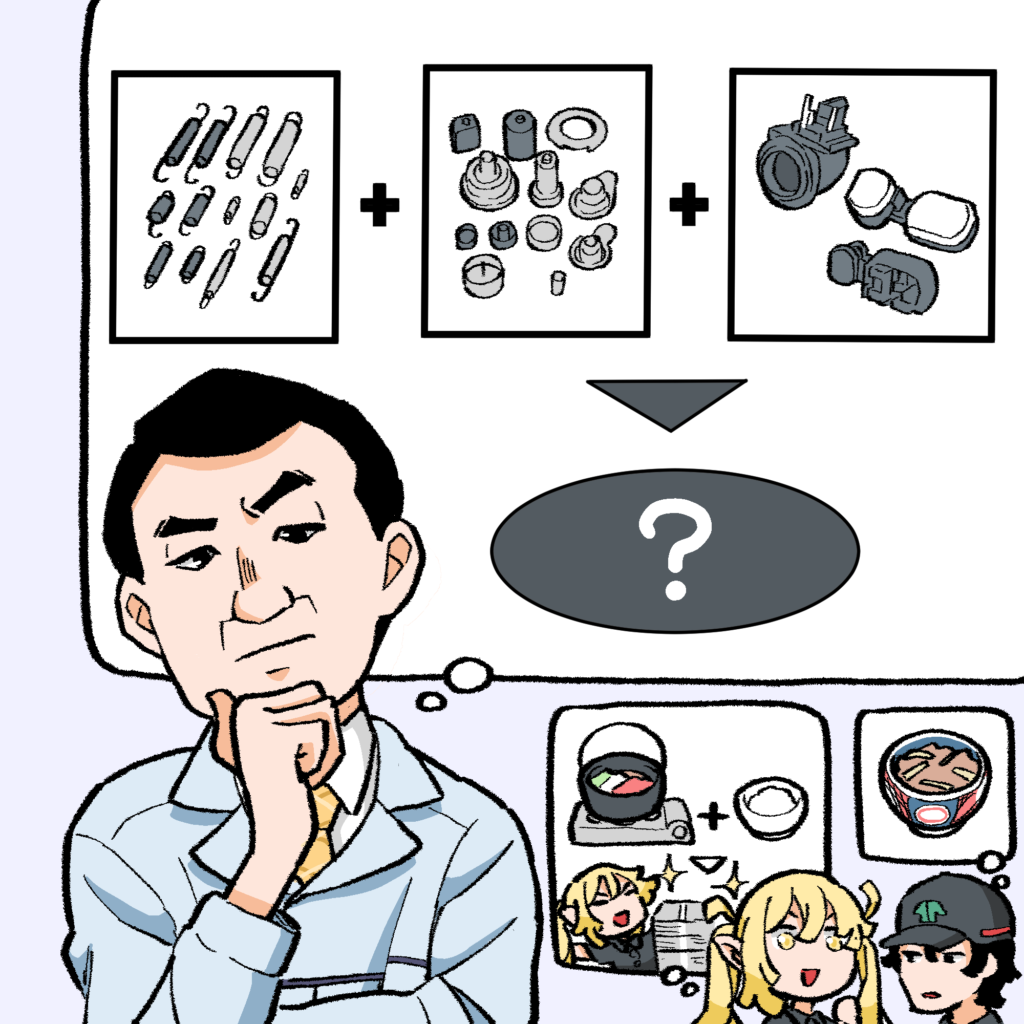
Adachi:
Resolvers are “rotation angle sensors” in simple terms. For example, it is an indispensable technology for controlling the rotation of the motor at the heart of HVs (hybrid vehicles), EVs (electric vehicles), and FCVs (fuel cell vehicles). It is said that this technology will become important not only for automobiles but also for robots and various other industries in the future, and I specialized in industrial resolvers in my previous job.
Yamakawa:
Mr. Tagawa gave us a lot of advice from the “onsite viewpoint,” a perspective that we in development are not aware of. This is a perspective that is absolutely necessary for mass production.
The Development Section and Prototype Section work together to face the challenges.
Yamakawa:
The development of an industrial resolver is a new challenge, but in order for customers to actually adopt it as a product, it must meet the requirements of “miniaturization,” “weight reduction,” “low cost,” and “environmental resistance” as a complete product. However, the development span of industrial products is very short, ranging from conception and study to mass production in one to two years. To achieve this, it was necessary for the entire team to share the same goals and work together as one.
Tagawa:
You are right, Mr. Yamakawa, and the project was realized because of the united efforts of all the specialists in each field.
In the prototyping section, two other people participated in the project besides me.
The team members are not dedicated to each process such as assembly, soldering, accuracy testing, and maintenance of standards, but are capable of handling all aspects of the work.
After a problem occurred, the members of the team analyzed the causes, and for problems that remained unresolved, we were able to work closely with the development section to share information and solve the problem.
Adachi:
My role was to ensure smooth communication between the Development Section and the Prototype Section. In many cases, newly designed prototypes in new fields do not go well when we try to assemble them out of the blue because we do not know how to do it, or there are problems with the equipment. We worked hard to resolve these issues.
Yamakawa:
When you first joined the team, your first task was to “reduce the accuracy measurement time” for industrial resolvers, wasn’t it?
Adachi:
Yes. We automated the measurement of accuracy, which until then had been very time-consuming and dependent on manual labor. In a limited development span like this project, we thought it was most important to be able to measure the detection accuracy of prototyped products as quickly as possible.
Yamakawa:
Mr. Adachi was really helpful in giving us an objective view of the project status based on his many years of experience. From that point on, the project progressed much faster.
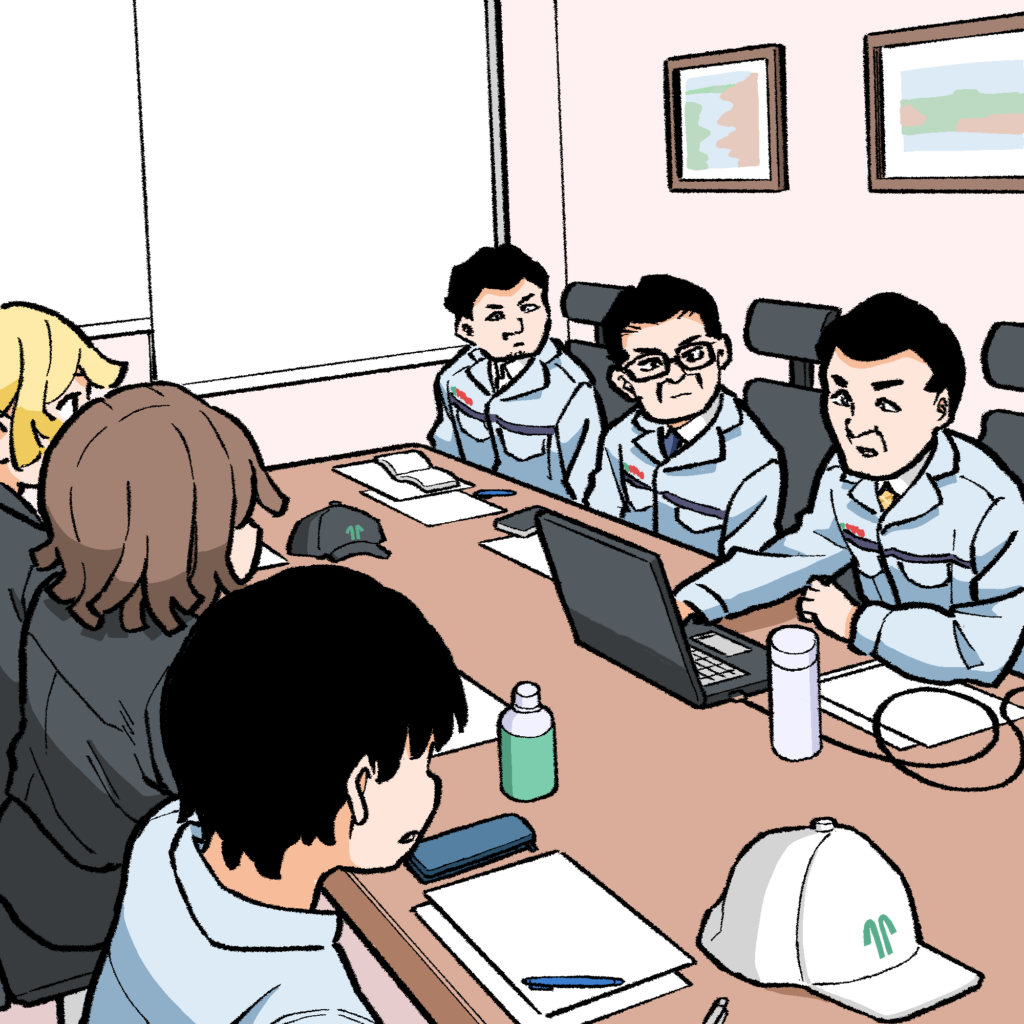
The project is halfway there, and we will do our best to further evolve it.
Yamakawa:
It has been about five years since we started. After all the hard work we had put in, we were thrilled when we were able to obtain an ideal waveform that could be used as a sensor. When the first industrial resolver was officially put on the market, we were all gut-punched. Thanks to our customers, we have been well received by them, especially for our quality control system that we have cultivated as an automotive parts manufacturer. The automotive industry is currently undergoing a major transformation that is said to occur only once every 100 years. It is exciting to think that this technology can contribute greatly to our company’s technological development!
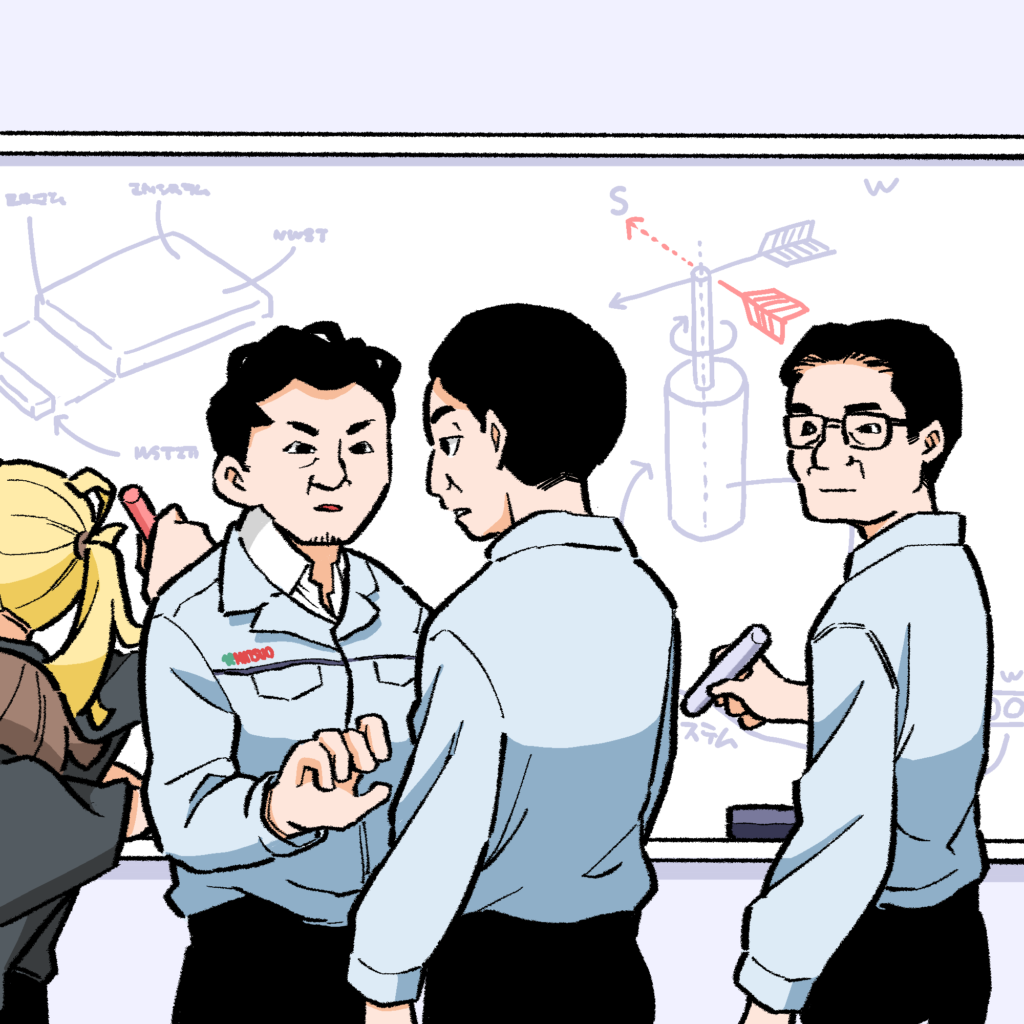
Adachi:
The project is still on its way. We are also preparing to develop a new micro resolver and have begun gathering information and conducting preliminary research. Thankfully, our customers have high expectations of us, and we will do our best to develop a resolver that meets their expectations. I would like to work at Matsuo Seisakusho, where I can work freely and spontaneously, and give back to society the knowledge and technology I have cultivated so far.
Tagawa:
The most interesting part of our job is “manufacturing where we have no experience. Currently, I hear that we have a good reputation with our customers, but I intend to further improve our work site without resting on our laurels. I hear that projects of this high degree of difficulty are coming up one after another in the future, so I would like to make the most of this experience and do my best to start up the project before mass production!