Progressive press

Forming press
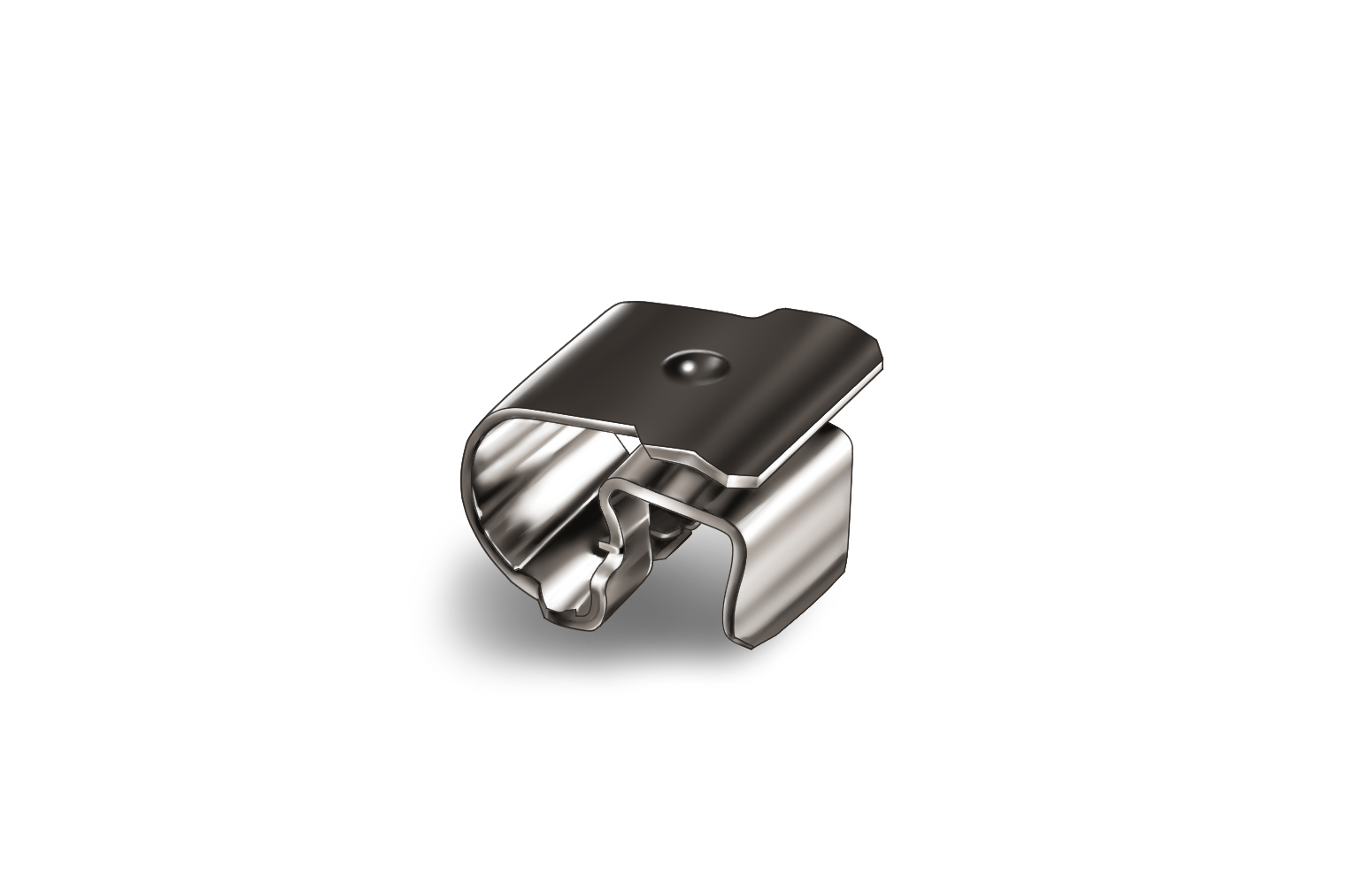
Transfer press
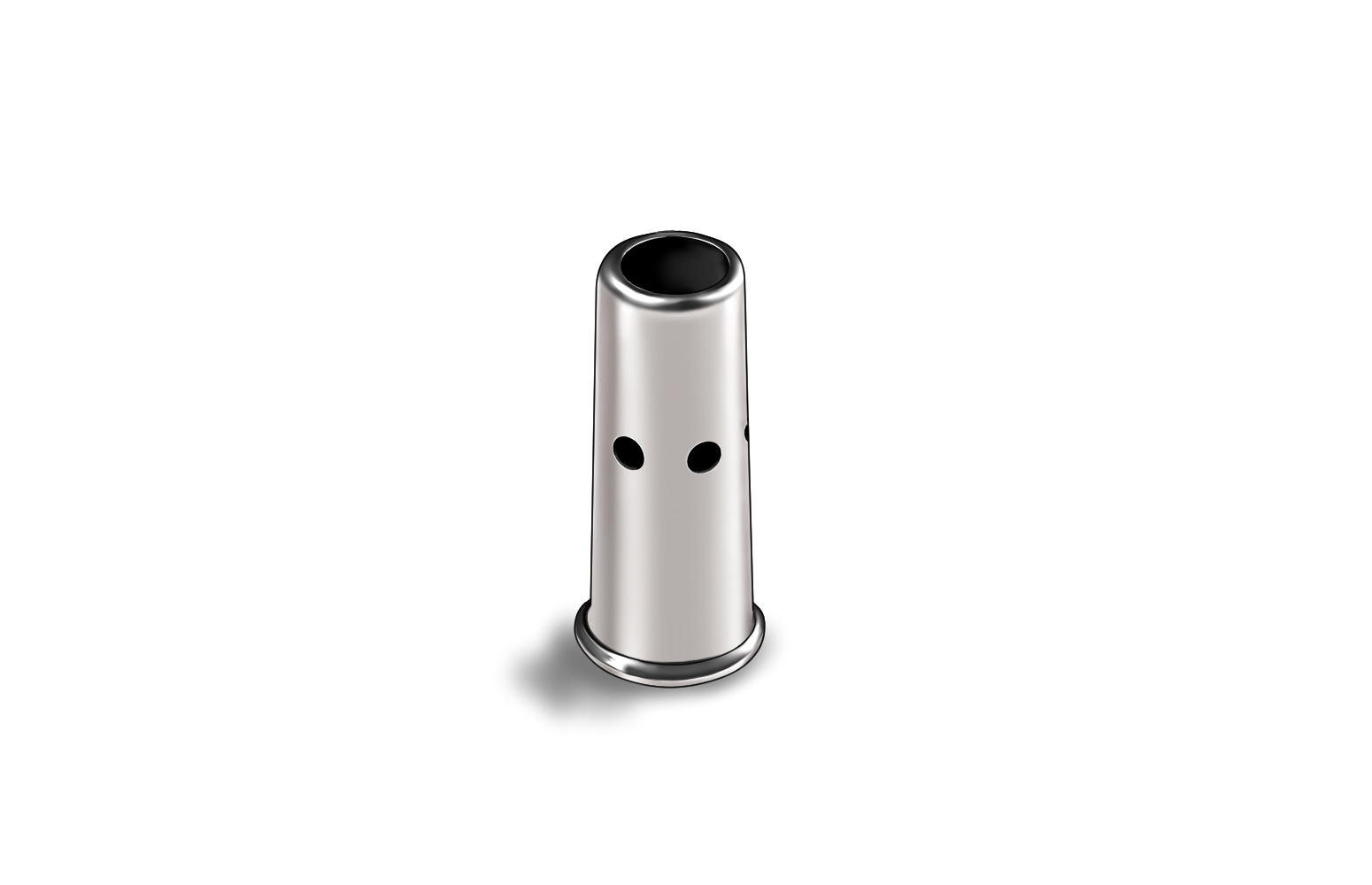
Cold forging press
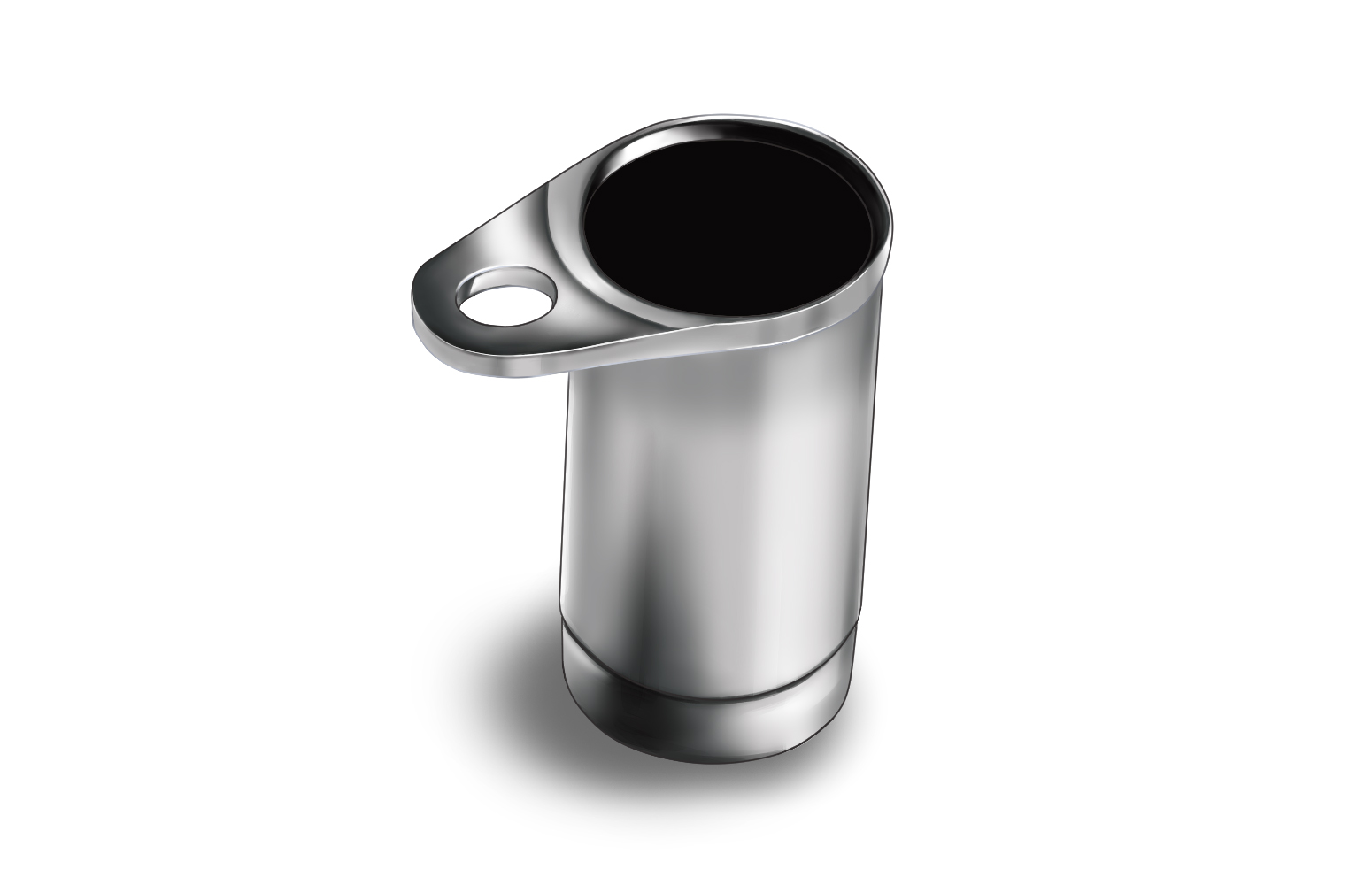
Multilayer pressed products
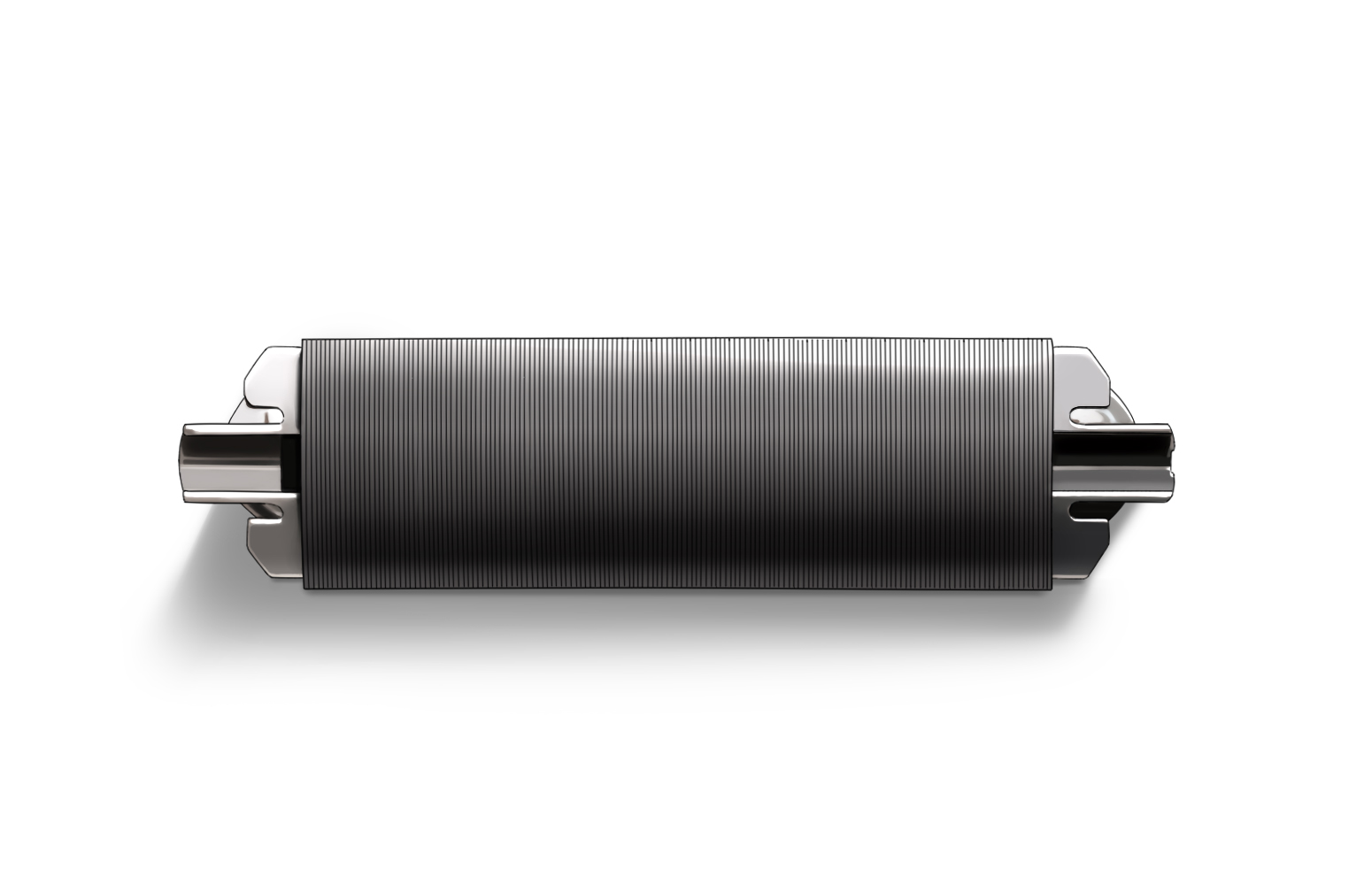
Precious metal plated products
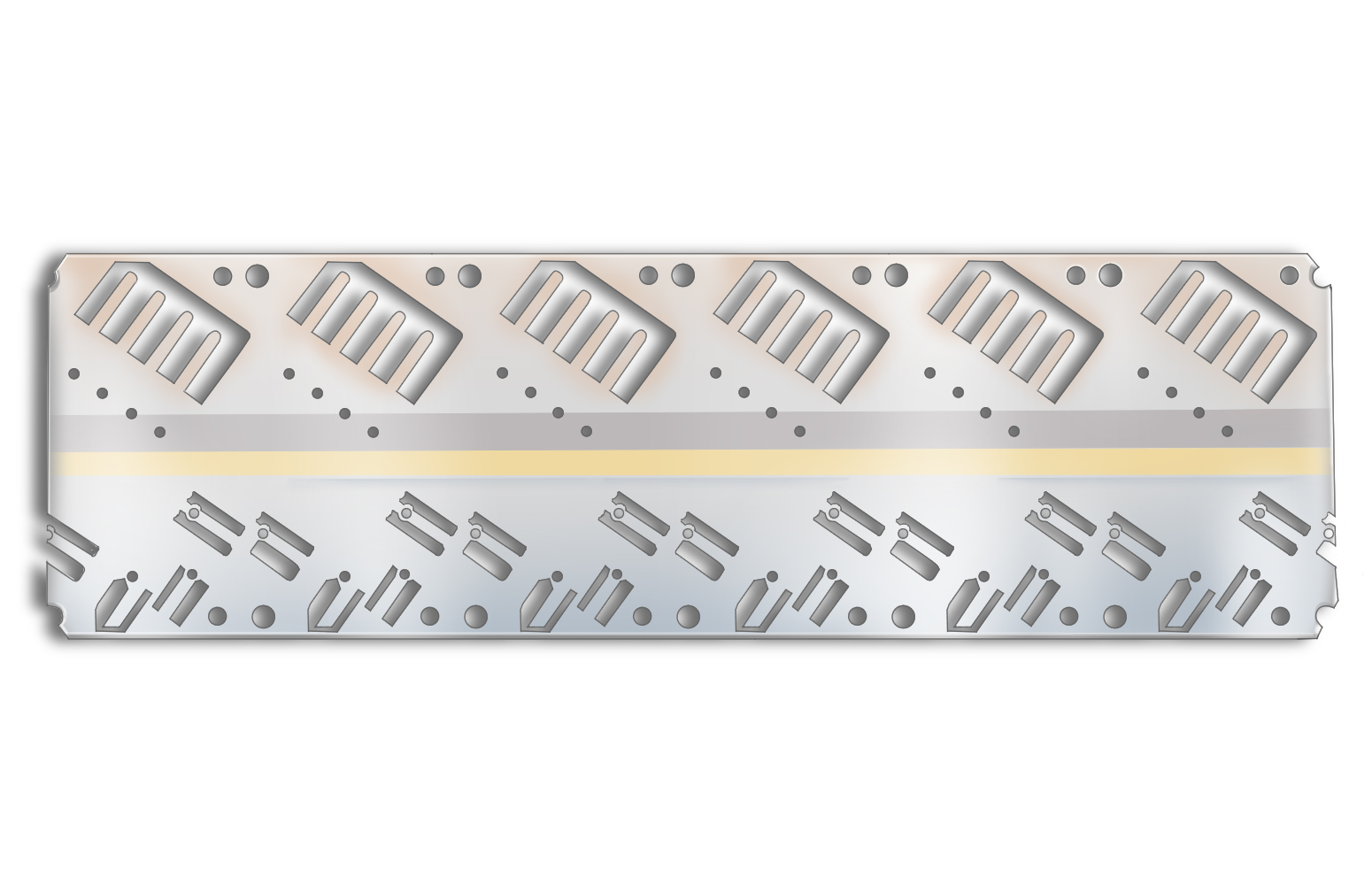
We accept orders from design consultation and prototyping of Precision Pressed Products.
- I want to make a part using Precision Pressed Products.
- We do not know the optimum material or shape for our product specifications.
- I have lost my original drawings.