LED lamp unit
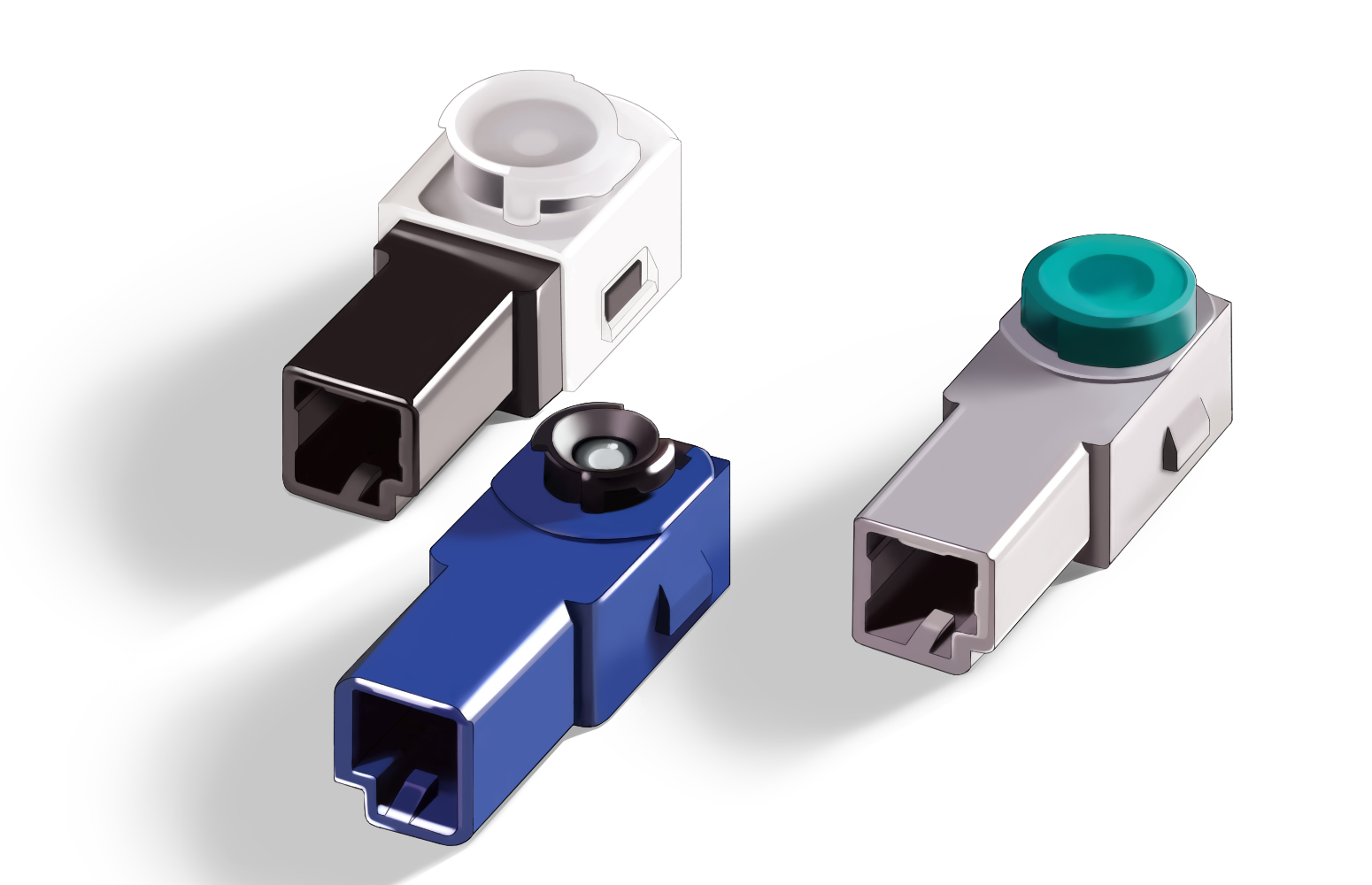
Air conditioner servo module
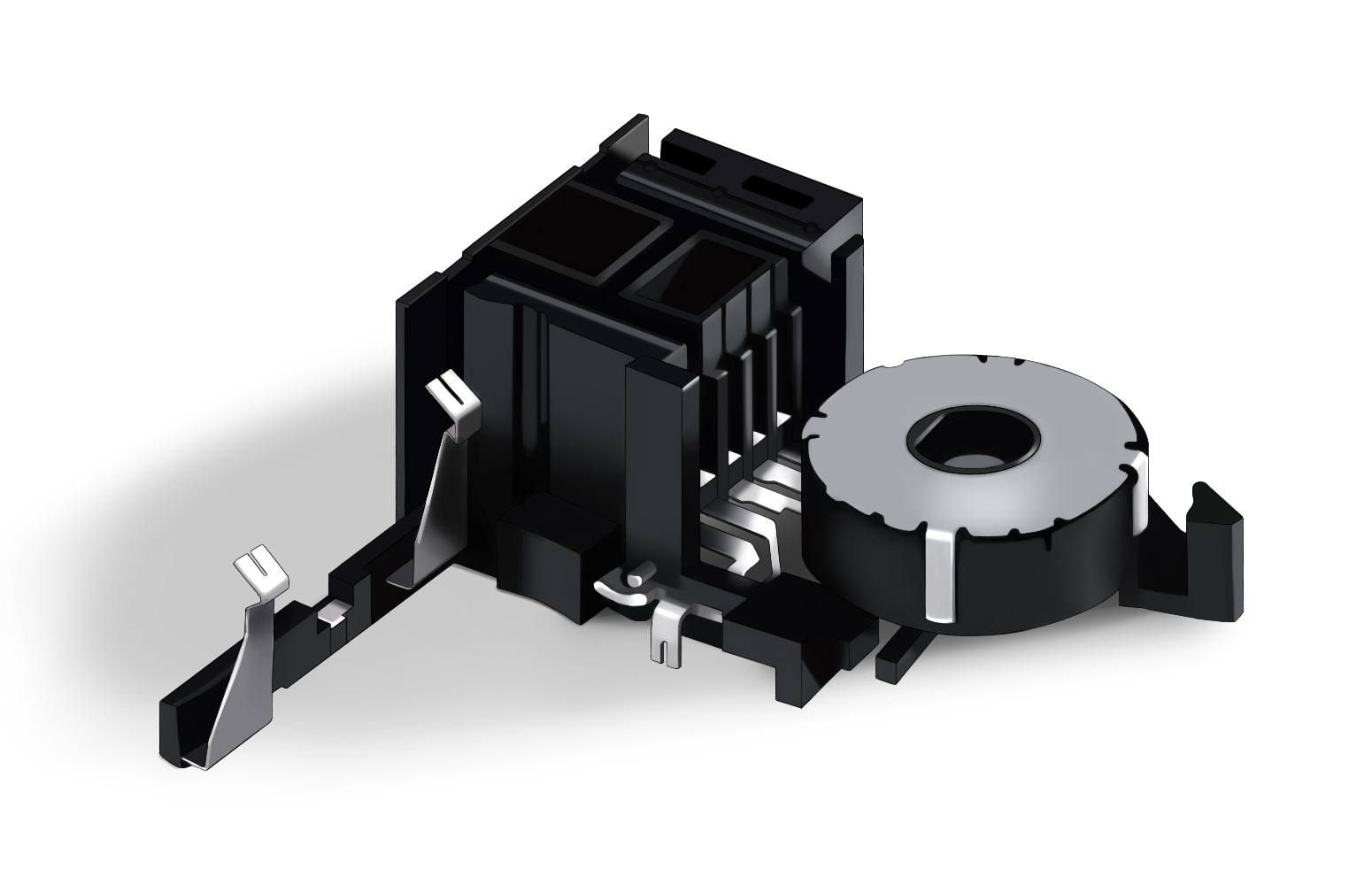
Power window unit
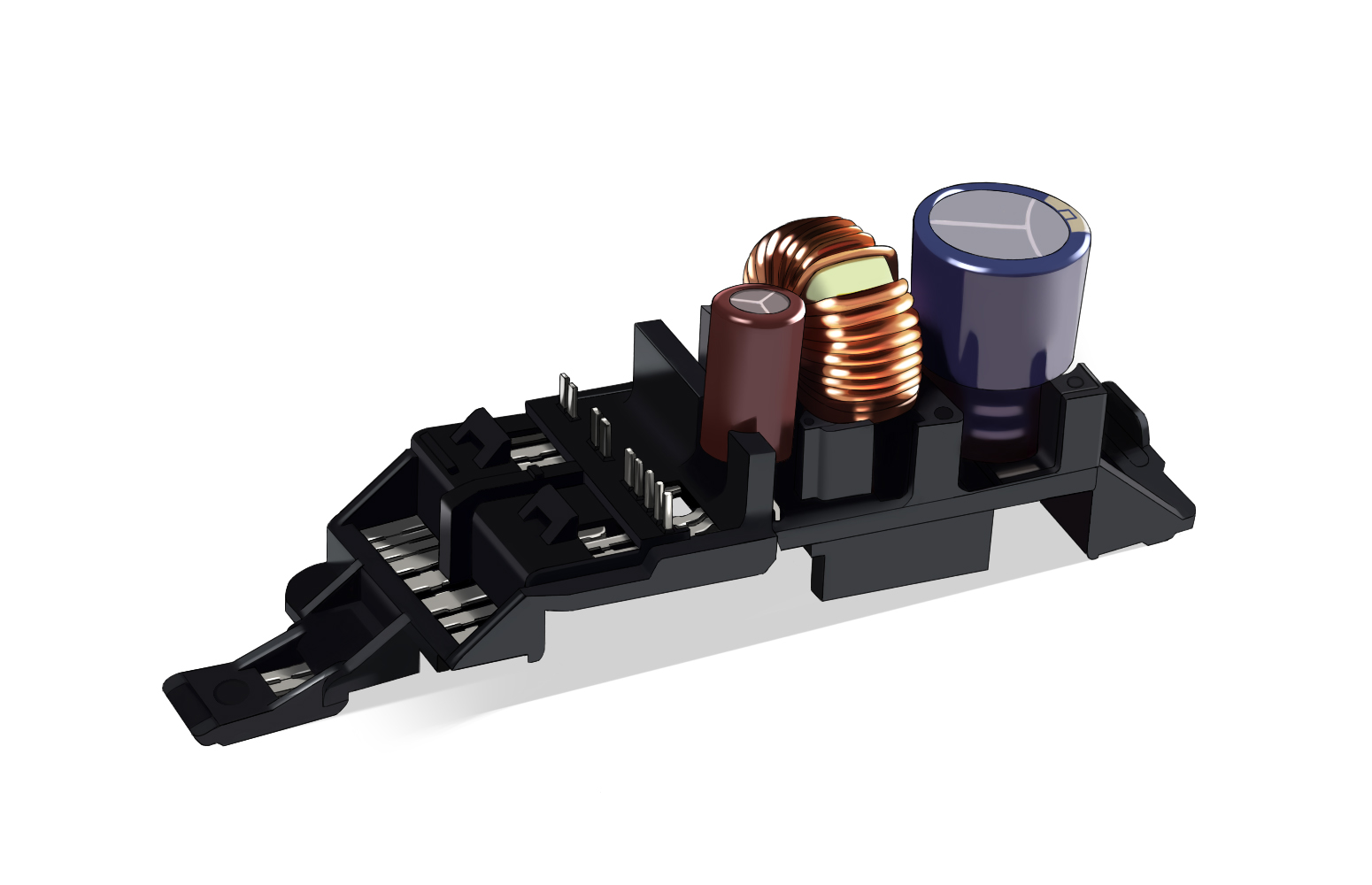
Compact horn switch
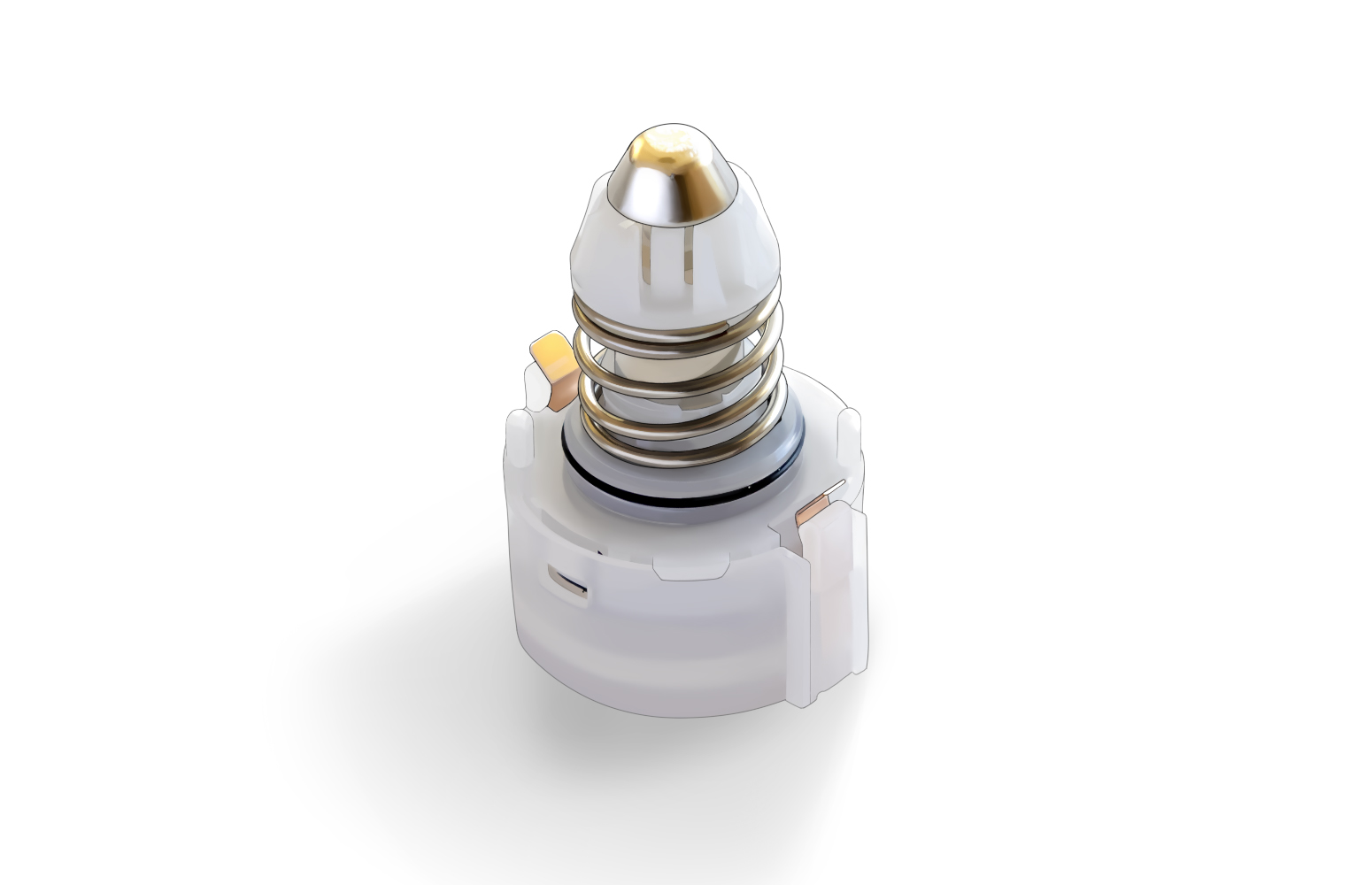
Stop lamp switch
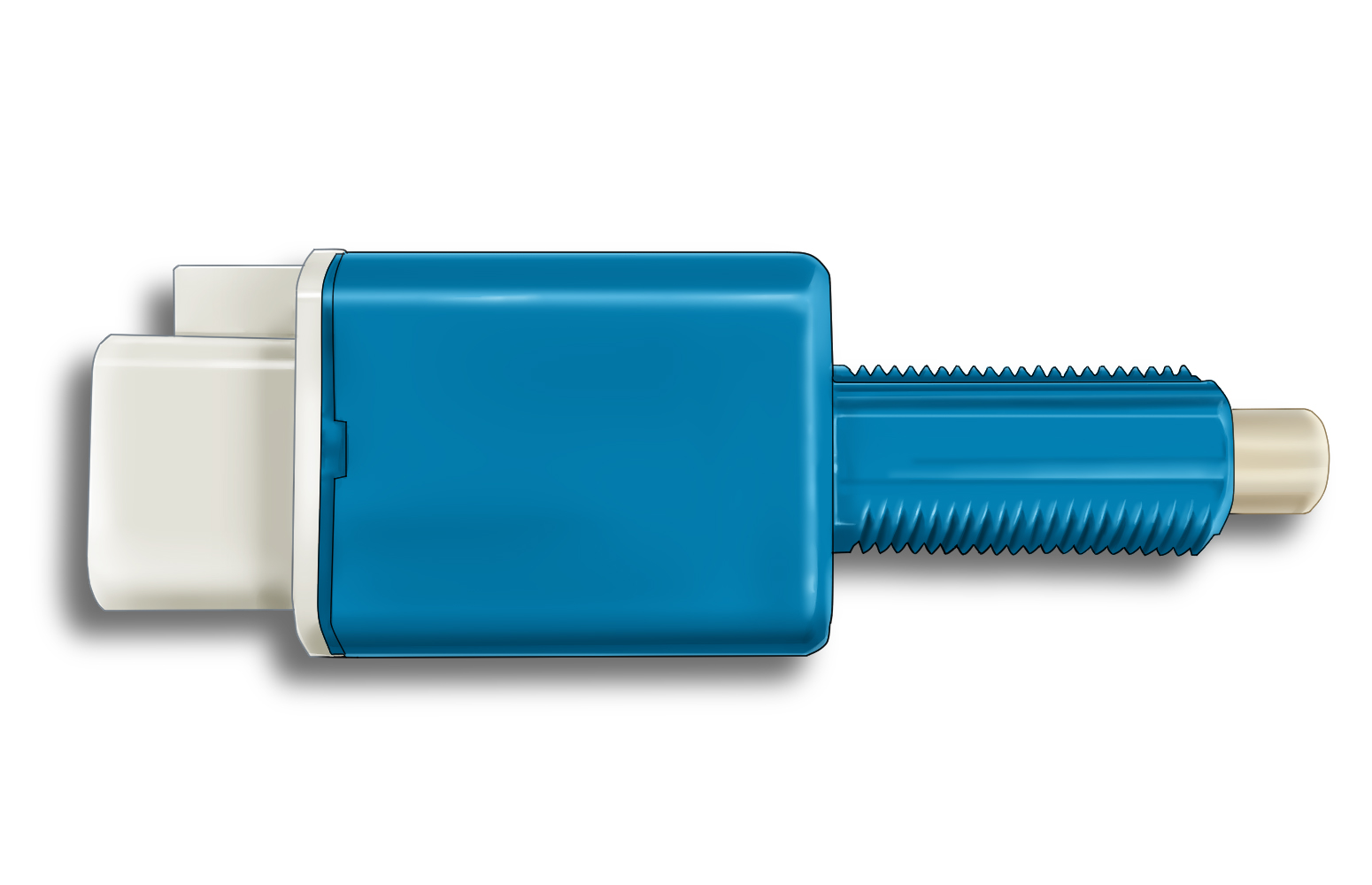
Holder brush
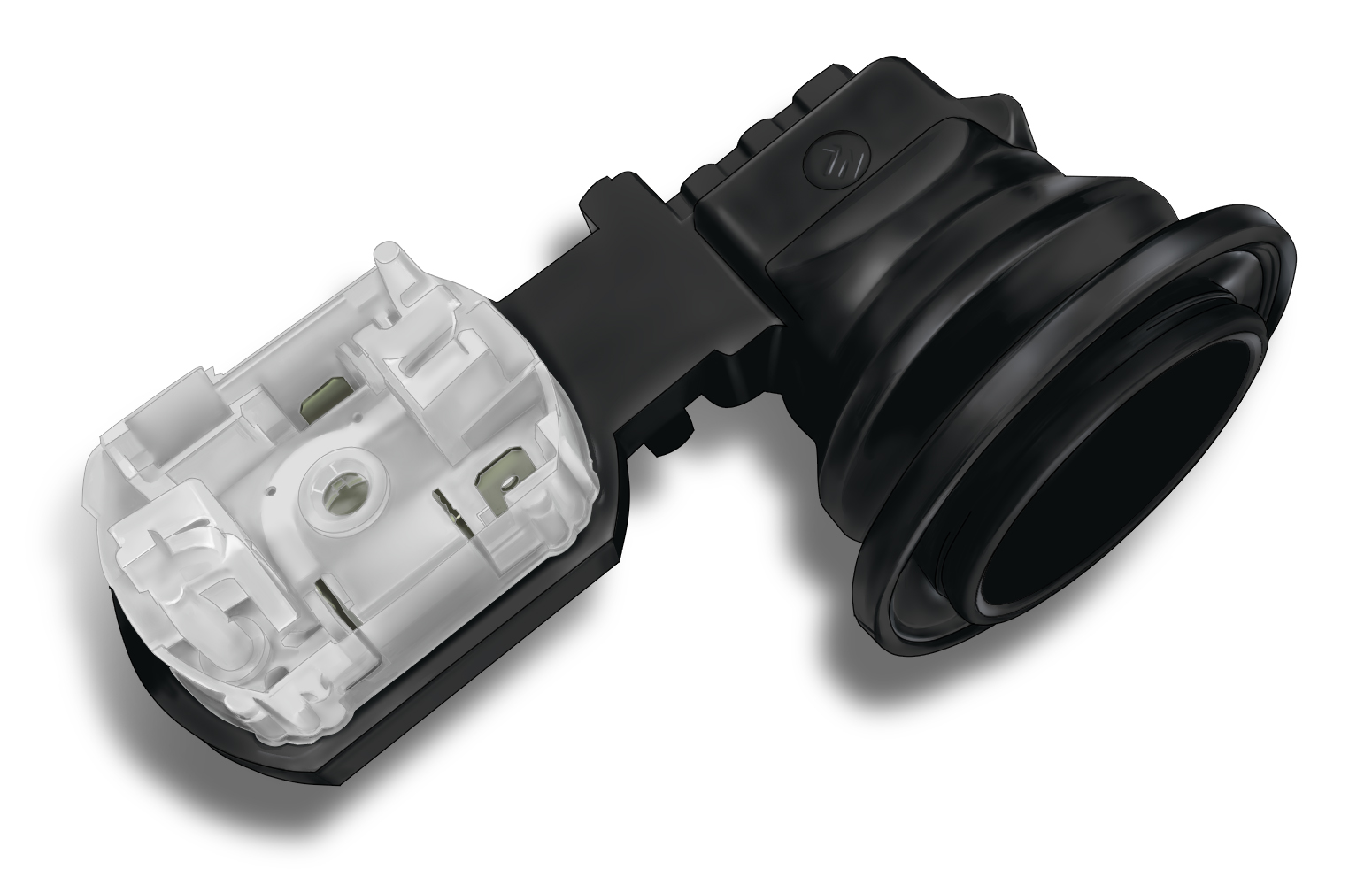
We accept orders from design consultation and prototyping of In-vehicle HMI unit.
- I want to make a part using In-vehicle HMI unit.
- We do not know the optimum material or shape for our product specifications.
- I have lost my original drawings.